5 Whys Root Cause Analysis
Introduction:
In the realm of problem-solving methodologies, the 5 Whys technique stands as a stalwart approach revered for its simplicity yet profound effectiveness. Originating from the Toyota Production System, this method has transcended industrial boundaries to become a fundamental tool in various fields, from manufacturing to software development and beyond. By delving deep into the layers of causality, the 5 Whys method uncovers the root causes behind issues, paving the way for sustainable solutions. In this article, we’ll explore the essence of 5 Whys Root Cause Analysis, its applications, and why it remains an indispensable tool in the arsenal of problem solvers worldwide.
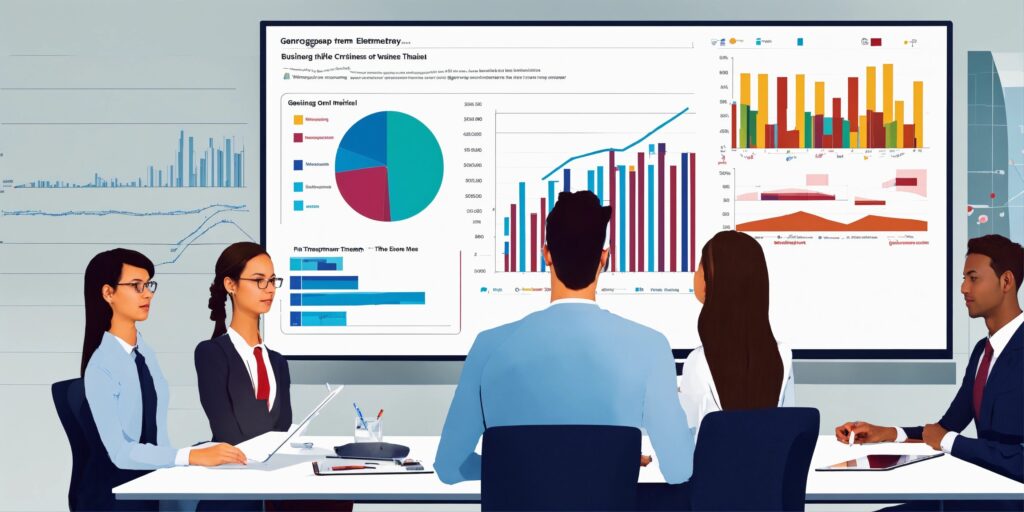
Understanding 5 Whys Root Cause Analysis: At its core, the 5 Whys technique is a systematic approach aimed at identifying the underlying causes of a problem by repeatedly asking the question “why?” Each iteration peels back a layer of causality, probing beyond the surface-level symptoms to uncover the root cause driving the issue. By asking “why” five times, practitioners navigate through the complexities of the problem landscape, arriving at a deeper understanding of the underlying factors at play.
The Process in Action: Let’s illustrate the 5 Whys method with a hypothetical scenario:
Problem: Production output has decreased.
- Why has production output decreased?
- Because the machine broke down.
- Why did the machine break down?
- Because it wasn’t maintained regularly.
- Why wasn’t the machine maintained regularly?
- Because maintenance schedules were not updated.
- Why weren’t maintenance schedules updated?
- Because there was no automated system in place to track them.
- Why was there no automated system in place?
- Because there was a lack of investment in modernizing maintenance processes.
In this example, the root cause of decreased production output is not the machine breakdown itself but rather the underlying issue of inadequate investment in modernization.
Key Principles and Benefits: The strength of the 5 Whys method lies in its simplicity and flexibility. It encourages a structured approach to problem-solving while allowing for adaptability to different contexts and complexities. Some key principles and benefits include:
- Simplicity: The straightforward nature of the technique makes it accessible to individuals at all levels of an organization.
- Deep Understanding: By systematically peeling back layers of causality, the method fosters a holistic understanding of problems, enabling more effective solutions.
- Proactive Problem Solving: Rather than merely addressing symptoms, the 5 Whys method targets root causes, helping prevent recurrence of issues.
- Cost-Efficiency: By tackling issues at their core, organizations can avoid wasted resources spent on treating symptoms.
- Continuous Improvement: Root cause analysis is integral to the philosophy of continuous improvement, driving organizational learning and growth over time.
Applications Across Industries: The versatility of the 5 Whys method lends itself to a myriad of applications across industries:
- Manufacturing: Identifying the root causes of defects, equipment failures, or production delays.
- Healthcare: Analyzing medical errors, patient safety incidents, or process inefficiencies.
- Information Technology: Investigating software bugs, system downtime, or cybersecurity breaches.
- Customer Service: Understanding the underlying reasons behind customer complaints or service failures.
- Project Management: Addressing project delays, budget overruns, or scope creep.
Conclusion:
In an ever-evolving landscape where challenges abound, the 5 Whys Root Cause Analysis stands as a beacon of clarity amidst complexity. By peeling back the layers of causality, this method empowers organizations to confront problems head-on, fostering a culture of proactive problem-solving and continuous improvement. As we navigate the intricacies of the modern world, the 5 Whys technique remains a steadfast ally in the pursuit of excellence and innovation.
Important Articles

Business Analyst , Functional Consultant, Provide Training on Business Analysis and SDLC Methodologies.
Thank you for reaching out! If you have any specific questions or topics in mind, please feel free to share them, and I’ll do my best to assist you. Whether you’re curious about a particular technology, scientific concept, literary work, or anything else, I’m here to provide information, advice, or engage in a discussion. Don’t hesitate to let me know how I can help you further!
My brother suggested I might like this blog He was totally right This post actually made my day You can not imagine simply how much time I had spent for this info Thanks
Thank You